Article
Cover
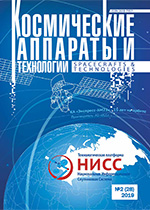
Title
Research and optimization of production cycle of high-precision composite spacecraft antenna reflectorAuthors
1N.А. Berdnikova, 1O.А. Belov, 2,3А.V. LopatinOrganizations
1JSC Academician M. F. Reshetnev Information Satellite SystemsZheleznogorsk, Krasnoyarsk region, Russian Federation
2Reshetnev Siberian State University of Science and Technology
Krasnoyarsk, Russian Federation
3Institute of Computational Technologies of SB RAS
Krasnoyarsk, Russian Federation
Abstract
The article presents a finite element model of CFRP (carbon fiber reinforcement material) reflector polymerization in autoclave for prediction of its shape after removing from the tool. The simulation was performed in the FEM software environment. The technique has developed in this work provides an opportunity to predict a shape and values of the production deformation of the reflector prior to its manufacture, and, if necessary, to introduce design and technological modifications. Successful verification of the finite-element modeling results of the reflector polymerization was performed using a full-scale experiment. Tool from CFRP has been created to forming the composite antenna reflector. This tool is cheaper than the Invar tool currently used. Also, the CFRP tool requires less time to manufacture. Recommendations for improving the technological process of composite contour antenna reflectors production manufactured on CFRP-tool are developed in the paper. The optimum curing mode of the composite reflector is determined. The research results were used in the performance of experimental design work and in the manufacture of reflectors for the spacecraft.Keywords
spacecraft antenna, carbon fiber reinforcement material, production stress, autoclave, tool, finite element methodReferences
[1] Weitsman Y. Optimal Cool-Down in Linear Viscoelasticity // Journal of Applied Mechanics, 1980, 47(1), pp. 35–39.
[2] Hahn H. T, Pagano P. J. Curing stresses in composite laminates // Journal of Composite Materials, 1975, vol. 1, pp. 91–106.
[3] Li C., Wisnom M. R., Stringer L. G. Simulation of process-induced residual stresses in thick filament wound tubes / Fourth Joint Canada-Japan Workshop on Composites, Vancouver, 2002.
[4] Rabearison N., Jochum C., Grandidier J. C. A FEM coupling model for properties prediction during the curing of an epoxy matrix // Computational Materials Science, 2009, vol 45, pp. 715–724.
[5] Gower M. R. L., Shaw R. M., Wright L., Urquhart J., Hughes J., Gnaniah S. Determination of ply level residual stresses in a laminated carbon fibre-reinforced epoxy composite using constant, linear and quadratic variations of the incremental slitting method // Composites: Part A, 2016, no. 90, pp. 441–450.
[6] Twarowski T. E., Lin S. E., Cell P. H. Curing in thick composite laminates experiment and simulation // Journal of Composite Materials, 1993, no. 27, pp. 215–250.
[7] Bogetti T., Gillespie J. Two-dimensional cure simulation of thick thermosetting composites // Journal of Composite Materials, 1991, no. 25, pp. 239–273.
[8] Hojjati M., Hoa S. Curing simulation of thick thermosetting composites // Composites Manufacturing, 1994, pp. 159–169.
[9] Hudek M. Examination of heat transfer during autoclave processing of polymer composites / Master’s thesis, Canada, 2001.
[10] Monaghan P. F., Brogan M. T., Oosthuizen P. H. Heat transfer in an autoclave for processing thermoplastic composites // Composites Manufacturing, 1991, no. 2, pp. 233–242.
[11] Loos A. C., Springer G. S. Curing of epoxy matrix composites // Journal of Composite Materials, 1983, no. 17, pp. 135–169.
[12] Dumont F., Frohlingsdorf W., Weimer C. Virtual autoclave implementation for improved composite part quality and productivity // CEAS Aeronautical Journal, 2013, no. 4, pp. 277–289.
[13] Weber T. A., Arent J.-C., Munch L., Duhovic M., Johannes M. A fast method for the generation of boundary conditions for thermal autoclave simulation // Balvers Composites: Part A, 2016, no. 88, pp. 216–225.
[14] ANSYS Inc. Available at: https://www.ansys.com (accessed: 21.05.2019)
[15] Altair Engineering. Available at: https://www.altairhyperworks.com (accessed: 21.05.2019)
For citing this article
Berdnikova N.А., Belov O.А., Lopatin А.V. Research and optimization of production cycle of high-precision composite spacecraft antenna reflector // Spacecrafts & Technologies, 2019, vol. 3, no. 2, pp. 59-72. doi: 10.26732/2618-7957-2019-2-59-72
This Article is licensed under a Creative Commons Attribution-NonCommercial 4.0 International License (CC BY-NC 4.0).