Article
Cover
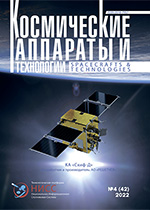
Title
Features of the development of a simulation model of the gearbox assembly of the spacecraft driveAuthors
1A.V. Gorbunov, 1O.I. Zheltyshev, 1A.S. Sablin, 1M.A. Zagainov, 2S.A. KuznetsovOrganizations
1Baltic State Technical University «VOENMEH» named after D. F. UstinovSaint Petersburg, Russian Federation
2JSC «Academician M. F. Reshetnev» Information Satellite Systems»
Zheleznogorsk, Krasnoyarsk region, Russian Federation
Abstract
The gear assembly of the rotational motion drive of the spacecraft system is considered. Such gear assemblies are one of the main elements of spacecraft systems with the use of large-sized structures that are folded in the transport position. Due to the development of computer technology, it becomes possible to create more accurate simulation models of such structures. The aim of the work is to create a simulation model that allows to analyze emerging loads on a wave transmission, which is part of the gear assembly of the spacecraft drive. Section one discusses the process of creating a finite element model of the drive. One of the features of creating a finite element model is a method of taking into account the preliminary stress-strain state in the structural elements of the wave transmission. Section two analyzes the data obtained during the calculation. The obtained equivalent stresses on the structural parts, contact stresses in the gear engagement are investigated, the torsional rigidity of the gearbox elements is determined, various tooth positions are considered during movement. The influence of loads applied to the output link of the gearbox on the surface of the gears is investigated. The obtained simulation model allows us to consider similar gear assemblies in which wave transmissions are used.Keywords
gearbox, drive, spacecraft, finite element method, strengthReferences
[1] Chaosheng S. Parameter design of double-circular-arc tooth profile and its influence on meshing characteristics of harmonic drive. Mechanism and Machine Theory, 2022. 167 p.
[2] Ishikawa S. Strain wave gearing having double-contact negative deflection tooth profile. Patent no. 9746065B2 US. 2013.
[3] Routh B. Design aspects of harmonic drive gear and performance improvement of its by problems identification: A review // AIP Conference Proceedings 1943, 2018, 020016. doi: 10.1063/1.5029592.
[4] Wael A. A. Using ANSYS for Finite Element Analysis. Momentum Press, 2018, vol. 2. 240 p.
[5] Yague-Spaude E. Computational Design, Simulation of Meshing, and Stress Analysis of Strain Wave Gear Drives. Rochester Institute of Technology, 2021.
[6] Ginzburg E. G., Golovanov N. F., Firun N. B., Khalebsky N. T. Zubchatye peredachi [Gears]. Leningrad, Mashinostroenie, 1980, 416 p. (In Russian)
[7] Gorbunov A. V., Korotkov E. B., Slobodzyan N. S. Vysokotochnaya sistema navedeniya i orientacii kosmicheskih bortovyh priborov na baze geksapoda s prostranstvennym datchikom polozheniya [High-precision space on-board instruments aiming and orientation system of the hexapod with a spatial position sensor] // Issues of Radioelectronics, 2017, no. 7, pp. 42–47. (In Russian)
[8] Kudryavtsev V. N., Kirdyashev Yu. N., Ginzburg E. G. Planetarnye peredachi [Planetary transmissions]. Leningrad, Mechanical Engineering, 1977, 536 p. (In Russian)
[9] Matveev S. A., Gorbunov A. V., Nadezhin M. I., Tolmachev A. S., Shirshov A. D., Yakovenko N. G. Precizionnye mekhatronnye ustrojstva i robototekhnicheskie kompleksy na ih osnove [Precision mechatronic devices and robotic complexes based on them] // Robotization of the Armed Forces of the Russian Federation. Collection of articles of the V Military-scientific conference, Anapa, 2020, pp. 201–203. (In Russian)
[10] Yangulov V. S. Volnovye i vintovye mekhanizmy i peredachi [Wave and screw mechanisms and gears]. Tomsk, Publishing House of Tomsk Polytechnic University, 2011, 184 p. (In Russian)
For citing this article
Gorbunov A.V., Zheltyshev O.I., Sablin A.S., Zagainov M.A., Kuznetsov S.A. Features of the development of a simulation model of the gearbox assembly of the spacecraft drive // Spacecrafts & Technologies, 2022, vol. 6, no. 4, pp. 255-262. doi: 10.26732/j.st.2022.4.04
This Article is licensed under a Creative Commons Attribution-NonCommercial 4.0 International License (CC BY-NC 4.0).