Article
Cover
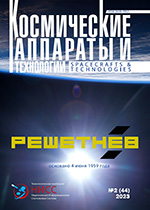
Title
Digital twin in the system of external adaptive control of robot manipulatorsAuthor
M.V. KubrikovOrganization
Reshetnev Siberian State University of Science and TechnologyKrasnoyarsk, Russian Federation
Abstract
The article discusses the implementation of a digital twin in the system of adaptive control of robotic manipulators. The use of digital twins to plan, control and maintain the life cycle of production equipment forms the sustainable introduction of robotic systems into the technological processes of high-tech enterprises. The use of a digital twin in the collaboration of a robot system allows you to design more versatile workplaces and assembly lines, and optimize their workload. A new approach is proposed that allows solving problems of direct and inverse kinematics for robotic manipulators. The approach is to represent the kinematic diagram of a robotic arm with six rotational joints as a vector model. Due to the low computational load, the use of the proposed approach in control systems makes it possible to reduce delays when working in real time, with the ability to increase the number of robotic arms and control with higher accuracy.Keywords
digital twin, production line, assembly, robotics, automation, production processReferences
[1] Rayankula V., Pathak P., Junco S. Inverse kinematics of mobile manipulator using bidirectional particle swarm optimization by manipulator decoupling // Mechanism and Machine Theory, 2019, vol. 131, pp. 385–405. doi: 10.1016/j.mechmachtheory.2018.09.022.
[2] Zhang T., Cheng Yo., Wu H., Yan Sh., Handroos H., Zheng L., Ji H., Pan P. Dynamic accuracy ant colony optimization of inverse kinematic (DAACOIK) analysis of multi-purpose deployer (MPD) for CFETR remote handling // Fusion Engineering and Design, 2020, vol. 156, P. 111522. doi: 10.1016/j.fusengdes.2020.111522.
[3] Yiyang L., Xi J., Hongfei B., Zhining W., Liangliang S. A General Robot Inverse Kinematics Solution Method Based on Improved PSO Algorithm // IEEE Access, 2021, vol. 9, pp. 32341–32350. doi: 10.1109/ACCESS.2021.3059714.
[4] World’s Top 10 Industrial Robot Manufacturers. Available at: https://www.marketresearchreports.com/blog/2019/05/08/world%E2%80%99s-top-10-industrial-robot-manufacturers (accessed 01.03.2023).
[5] Tong Yu., Liu J., Liu Yu., Yuan Yu. Analytical inverse kinematic computation for 7-DOF redundant sliding manipulators // Mechanism and Machine Theory, 2021, vol. 155, P. 104006. doi: 10.1016/j.mechmachtheory.2020.104006.
[6] Li J., Yu H., Shen N., Zhong Zh., Lu Yi., Fan J. A novel inverse kinematics method for 6-DOF robots with non-spherical wrist // Mechanism and Machine Theory, 2021, vol. 157, P. 104180. doi: 10.1016/j.mechmachtheory.2020.104180.
[7] Xiao F., Li G., Jiang D., Xie Yu., Yun J., Liu Yi., Huang L., Fang Z. An effective and unified method to derive the inverse kinematics formulas of general six-DOF manipulator with simple geometry // Mechanism and Machine Theory, 2021, vol. 159, P. 104265. doi: 10.1016/j.mechmachtheory.2021.104265.
[8] Lopez-Franco C., Hernandez-Barragan J., Alanis A. Y., Arana-Daniel N. A soft computing approach for inverse kinematics of robot manipulators // Engineering Applications of Artificial Intelligence, 2018, vol. 74, pp. 104–120.
[9] El-Sherbiny A., Elhosseini M. A., Haikal A. Y. A new ABC variant for solving inverse kinematics problem in 5 DOF robot arm // Applied Soft Computing Journal, 2018, vol. 73, pp. 24–38.
[10] Ryaben'kii V. S., Tsynkov S. V. A Theoretical Introduction to Numerical Analysis. New York : CRC Press, 2006, P. 243.
[11] Sauer T. Numerical Analysis (2nd ed.). Pearson Education Inc., 2005, P. 109.
[12] Pikalov I., Spirin E., Saramud M., Kubrikov M. Vector model for solving the inverse kinematics problem in the system of external adaptive control of robotic manipulators // Mechanism and Machine Theory, 2022, vol. 174, P. 104912. doi: 10.1016/j.mechmachtheory.2022.104912.
For citing this article
Kubrikov M.V. Digital twin in the system of external adaptive control of robot manipulators // Spacecrafts & Technologies, 2023, vol. 7, no. 2, pp. 171-176. doi: 10.26732/j.st.2023.2.10
This Article is licensed under a Creative Commons Attribution-NonCommercial 4.0 International License (CC BY-NC 4.0).